In an effort to take some of the strain off staff working in manual assembly and boost efficiency in its production processes, item has developed an innovative, modular collaborative robot assembly system. Staff can reconfigure it in seconds and stow everything away neatly when not in use. Small batch sizes can therefore be assembled on a (semi-)automated but cost-effective basis.
This user report shows you how the development team turned an idea into an efficient solution that can be continuously expanded. Be inspired by this success story and discover the potential and opportunities that a similar system could offer your company.
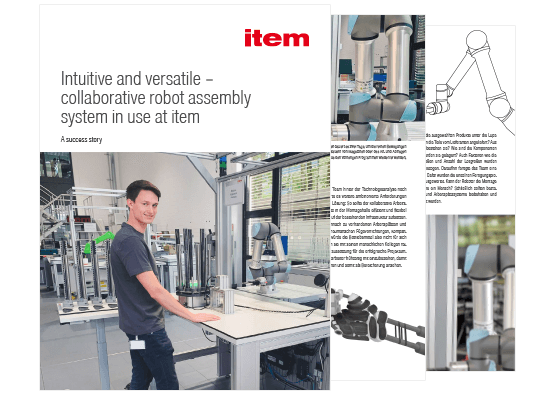
Human-robot collaboration
Efficient assembly – even for the smallest of series
What makes the item solution special
Unlike other solutions, the item system is not permanently mounted on a work bench – it’s connected to a fixture that can be docked with various different workstations. The work bench itself can also be very quickly and flexibly adapted to different tasks. For instance, using a range of interchangeable panels means setup takes just seconds. This approach ensures that a manual assembly work bench can be reconfigured in seconds for (semi-)automated production – the production of parts that would be uneconomical to manufacture with a specially procured machine.
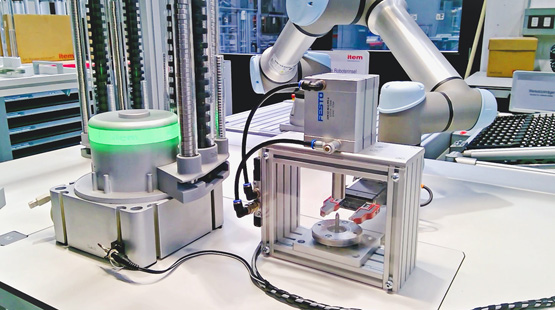
A close-up of the assembly system: The magazine (left) holds the individual components that the robot places into the assembly device. Both the magazine and the assembly device are installed on an interchangeable panel, which means the work bench can be changed over in seconds. The assembled products are set down on the workpiece carrier (rear right).
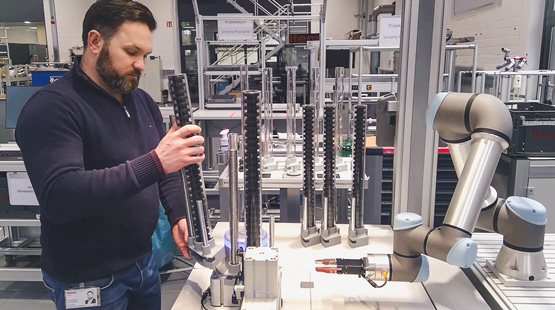
The worker loads the device with magazines. The robot then removes the individual components from these magazines. The component magazine is a custom component made specially on a 3D printer. The robot also mostly uses the same devices that staff use. This helps to avoid unnecessary expense on new purchases.
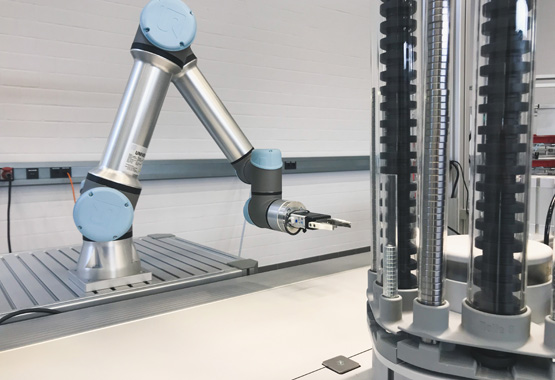
In-depth insight into development
Get the free user report now and find out more about the agile development process and the remarkable results.
For example, find out how …
- the collaborative assembly system also saves time in logistics and cuts packaging waste.
- the team managed to produce the first ready-to-sell batch with robot assistance only shortly after starting the project.
- item ensured high levels of acceptance by staff and how individual employees see their “new colleague”.
This type of solution can be implemented in your company, too!
Each item work bench system can be extended with a docking station for the collaborative robot assembly system. As a result, it can be used at as many item production sites as possible and also, further down the line, will give customers the option of implementing and using similar solutions based on item technology, too.
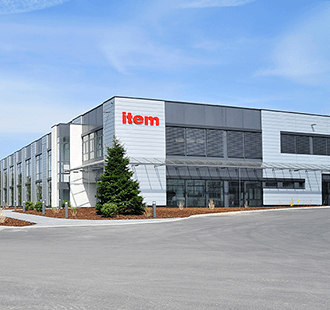
item Industrietechnik is the pioneer in building kit systems for industrial applications and a global market leader.
Experience
Selection & availability
Everything for state-of-the-art production
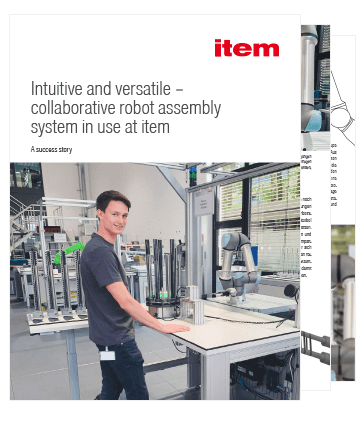
Valuable insights into the complete development process
Find out in the user report how item went about planning and developing the collaborative robot assembly system, how the system works in detail and why a similar solution could also be of interest for your company.